Everything You Need to Know About Linen
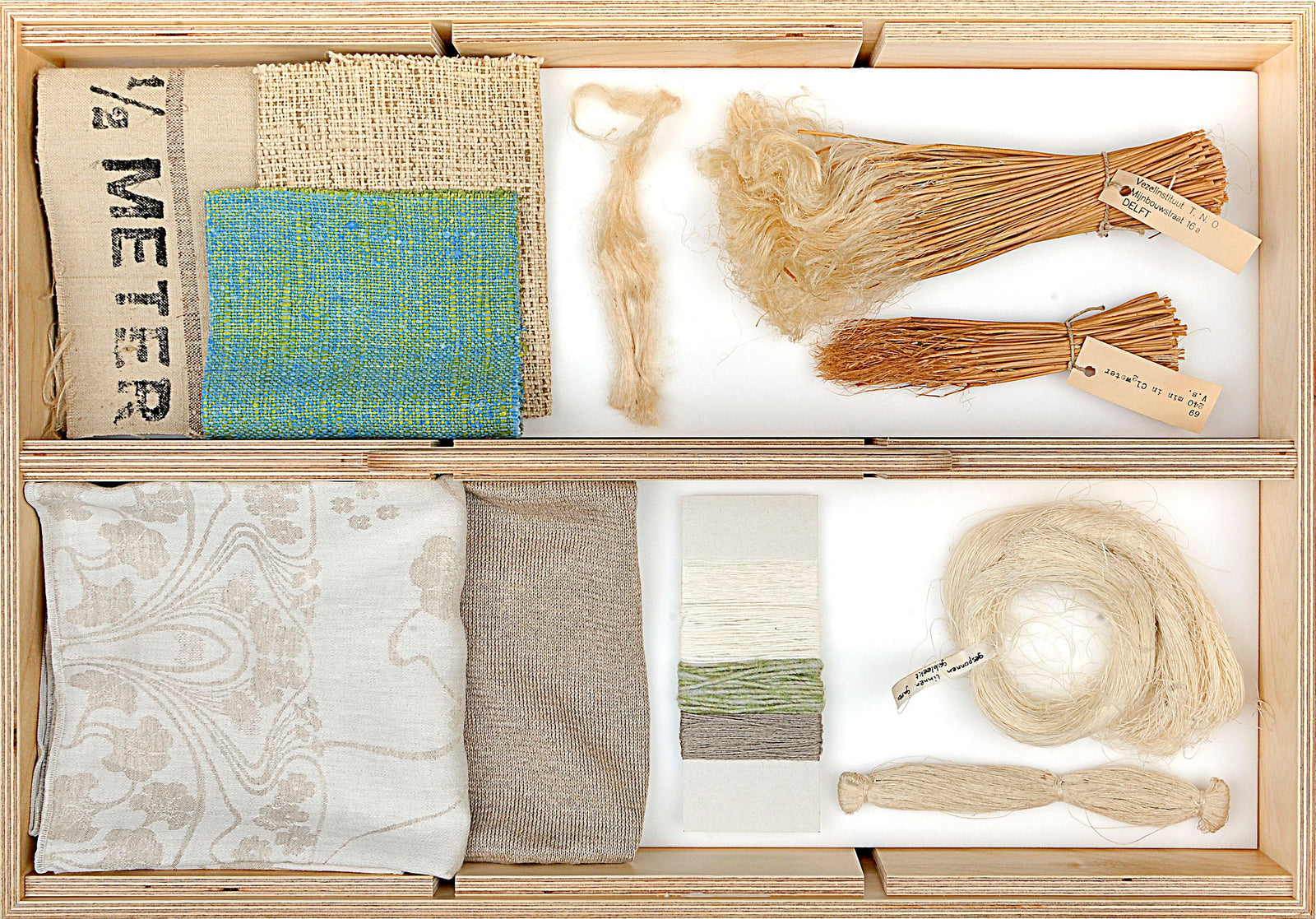
Linen is one of the most unique textiles out there. It's thin and breathable yet durable and protective against the sun’s rays. This makes it the perfect fabric to wear in sunny and hot areas. Linen also serves as a natural antiseptic, meaning no bacteria or fungus can live in the fabric. With all these pros, it's no wonder why this natural fabric is so popular.
I suppose it shouldn’t be surprising that the process to make such fabric at a high quality takes a lot of work. In this article, we’ll aim to answer all your questions of what, where, and how that you have about linen to the best of our abilities and according to our experience. It gets a bit scientific and complicated, but we’ll try our best to keep it simple and understandable!
What is Linen Made of?

Photo by Joep Vogels under creative commons license and layout by Simone de Waart
Linen is a natural fiber, which means it's made from a plant, naturally. The plant used is called a flax plant or, scientifically, Linum usitatissimum. Flax is actually one of the oldest plants cultivated in history. Thanks to that, linen became one of the oldest textiles man have made and used in the world.
Where is Linen Made?
Now that we know linen comes from a flax plant, next comes the question of where this flax is cultivated. Flax is a pretty easy going plant, almost able to be grown anywhere, except in extreme heat, without much care needed. However, flax for high quality linen needs a certain environment to flourish. The best flax for linen is grown in cool, damp areas with plenty of organic matter.
So, where are these environments exactly? High quality flax is primarily grown in Western Europe. The top quality linen producers are known to be Ireland, Italy, and Belgium, but more of Europe and Asia have been producing linen that is just as high in quality.
For example, Belarus, which is situated between Poland and Russia, is where our linen comes from and is even the national flower of the country, so I think it is safe to say they are confident in their flax production.
Flax flowers are also just cute and pretty.

Photo by Tish Steel under creative commons license
How is Linen Made?
Linen is used for a variety of products from napkins to bed sheets to dresses. It's pretty much a fabric that can be used for any textile product. Though the fabric is used for a variety of products, the process is pretty much the same for all of them until it comes to weaving the end product.
The start of the process is, of course, cultivating flax in an organic field.
Once ready, the flax is handpicked from the root up, which is important to keeping up the quality of the fibers. Farming machinery is still unable to preserve the roots during harvest, so manual labor is still needed in order to produce a harvest of the highest quality of linen fibers. Just to let you know ahead of time, you’ll see throughout the whole process that using machinery or chemicals is not the best option in creating top tier linen.
The next step is to dry the stalks. This usually takes several weeks, but once they are dried, flax then goes through a process called threshing.
Threshing is when the seeds are literally beaten out of the flax. The dried stalks are pulverized until all the seed pods are crushed, and the loose seeds are shaken out. It’s not quite as violent as described, but there is a lot of squishing and squashing.
After cleaning the stalks of seed remnants, the next part of the process involves a bit of biology.
Retting, to put it simply, is the process of rotting away the inner stalk to separate it from the outer stalk. This can be done in a number of ways, but the point is to have bacteria decompose the pectin, which is what essentially sticks the plant together. This process involves exposure to moisture that can last from days to weeks in order to burst the cells inside of the plant, which would allow for bacteria to make their way in and breakdown the pectin.
There are three main ways to ret linen: in slow-moving or stagnant bodies of water, fields, or tanks.
Water retting is the most used method because it produces the best linen fibers.
Water retting uses slow moving waters like ponds or streams. The flax is submerged in water, and the more stagnant and shallow the water is, the faster the process. But! Being faster is not necessarily a good thing.
Retting in absolutely stagnant water is not ideal as the fibers could easily be over-retted and is more likely to get dirty. The smell that's produced is also the worst in such a scenario. It is a bunch of plants rotting in stagnant water, after all. Thus, it’s best to use a stream even if it will take longer, but this is the way to get the best quality!

Photo by Rosser1954 under the creative commons license
Dew retting is a process that uses a field.
This method is usually used if there is no body of water available for water retting. It's also best used in regions with warm days and cool, moist nights to produce dew. The flax is evenly and thinly spread across a grassy field, allowing for exposure to the air, sun, and dew. This combination over the span of a few weeks causes the stem to dissolve.
Dew retting tends to produce lower quality linen fibers and are darker than water-retted fibers due to the sun exposure.

Photo by Stanzilla under creative common license
Tank retting comes off as the most mass productive option since it can be done any time of the year with consistent production times.
This method usually uses vats made of concrete. The flax is soaked in warm water for a few hours to remove dirt and pigment, and then the water is changed for the stalks to soak in for a few days. This method is similar to water retting in a stagnant body of water, but it is more industrialized and controlled.
There is one more method, but this one is the worse one to use. No one who cares about the end product would use this.
Just like water retting, the flax is submerged, but this time it's in a chemical solution. This method is the fastest, taking only a few hours, yet the downsides outweigh the almost comparatively instant production time. It's more expensive. It produces more pollution waste. To top it off, the quality is not that great.
It’s really just not worth it until the chemical solution is refined.
Moving on, the next step is to gather the fibers by separating them from the rest of the plant.
The retted stalks, now straw, are dried again to be scutched. Scutching is the way to remove any leftover straw and wood bits hanging on to the fiber. This can be done by hand or by machine, though it is obviously preferable to do so manually.
To scutch by hand, a wooden “knife” is used to scrape the fibers. The retted flax is hung vertically so that the leftovers can be pulled off the fibers and fall off. The fibers are scutched until the flax fibers are smooth and silky, and a person can only produce up to 15 pounds of flax a day.
How long it takes is very dependent on if the retting process of the fiber is done well or not. If over-retted, the fibers may break and crumble. If under-retted, the stalk can be hard to separate from the fibers, which can end up damaging the fibers.

Photo by Peter van der Sluijs under GNU free license
Scutching mills are much faster and cheaper, but it causes more waste.
One way machines are used to scutch is by crushing stalks between two metal rollers. This machine can produce around 150 pounds of flax fibers every hour, which is ten times a day of one person's manual scutching, but in an hour.
That’s mechanization for you.
After the flax has been scutched, heckling (can also be spelled as “hackling” or “hackeling”) is employed. Heckling is essentially combing the fibers, and this process is the last step in cleaning and prepping the fibers. A small bed of nails is used.
Yes, this bed of nails is considered a comb even if it looks too scary to be considered one.

Photo by Pymouss under GNU free license
Heckling splits and straightens the fibers while also removing any remaining impurities. Usually 3 different combs are used, each with a different number of nails per inch, progressing from coarser combs to finer ones. The finer the final comb, the finer the end product will be, so more combs are used depending on how fine a producer wants the fibers to be.
Now, we get to the spinning.
The flax fibers are hand spun using a distaff, which is a long vertical pole attached or next to a spinning wheel. The distaff keeps the fibers organized so that they don’t get all tangled during the spinning process.
The spinning process twists the fibers to form yarn, and then the yarn is winded onto a spool or something similar. It’s best to keep the fibers damp throughout the spinning process to prevent fly-away strands and create a smooth end product.

Photo by Virginia State Parks under creative commons license
Finally, once the yarn is done, it can be woven or knitted into fabrics! It’s a long journey to get to this stage.
And special to our linen collection, an herbal enzyme wash is used. Each piece of clothing is submerged in an herbal enzyme consisting of 26 different healing herbs. It’s this wash that is key to creating our soft yet robust linen clothing!
Curious About Us?
Down in the South, find us at Cella’s Boutique in New Orleans, LA. Our shop is in the French Quarter, so if you ever find yourself in the area, please come on in and see our linen clothing in person! You will also find we have much more to offer as well.